Manufacturing Equipment
Regardless of your production needs, Setpoint can design and build manufacturing equipment that assembles, tests and inspects your product. Our flexible and reliable solutions allow you to do the following:
- Accurately and consistently assemble to your specifications
- Use the same machine for multiple product platforms with quick change-out tooling
- Closely monitor the performance of each step to production
- Produce the highest quality products
Building Custom Manufacturing Equipment
No customer is exactly the same, so why should automated manufacturing solutions be the same? We have worked with a wide variety of customers in many different industries to design and build hundreds of custom machines that automate repetitive processes. Below is a small sampling of some of those solutions:
- Testing and Loading Machine. This station provided an electrical test on each incoming part and verified test results to ensure compliance to standards. Parts were then robotically offloaded into matrixes ready for downstream.
- Ammunition Back End Case Line Machine. Completely changing the way cases are produced, our 30’ x 30’ design includes two forming stations, a wash system, and annealing tower to provide cases ready to load.
- Case Mouth Waterproofing Machine. Apply waterproof to your cartridges.
- Label, Print & Apply. Operators can precisely, quickly, and consistently place sterilized barcode labels onto a wide range of part sizes with this machine. In 30 seconds, operators can change model configurations for an efficient changeover.
- Press Machine. A compact, portable pressing solution or large 30 ton press can permanently join two components to form unique subassemblies.
- Torque Assembly. A flexible torque station with a nesting system that can be changed out without the use of tools in less than 30 seconds and is flexible enough to handle future model configurations.
- Torque Station with Automatic Screw Feeder. We helped significantly reduce overall labor costs and repetitive motion injuries associated with manual assembly sequences with this machine. Each station includes an articulating arm that holds the torque tooling and allows the operator to easily manipulate it into place to install each fastener.
- Hydraulic Tube Swage Machine. This highly efficient and self-contained machine permanently swages the ends of precut steel tubing in less than 7 seconds per part. It can run continuously to meet the demands of the customer’s high-production throughput environment.
- Crimping Machine. This compact, ergonomic work station permanently, precisely, and quickly joins components into a subassembly. It has a wide range of removable change-out tooling to run a variety of products on a single machine.
Decreasing Cycle Time and Increasing ROI
One thing remains the same across all the solutions we create—each one solves issues. Each custom automated solution is focused on decreasing cycle time, waste (too much inventory, handling, etc.), rework, and labor minutes per unit while increasing your return on investment (ROI).
Setpoint is always up for a challenge. We have designed and built many different types of manufacturing equipment but we are most interested in what we can do to specifically help you to be more successful in your manufacturing operations. Call us today to talk about the custom manufacturing equipment you need.

Testing and Loading
This station provided an electrical test on each incoming part and verified test results to ensure compliance to standards. Parts were then robotically offloaded into matrixes ready for downstream.

Label Print & Apply
Operators can precisely, quickly, and consistently place sterilized barcode labels onto a wide range of part sizes with this machine. In 30 seconds, operators can change model configurations for an efficient changeover.
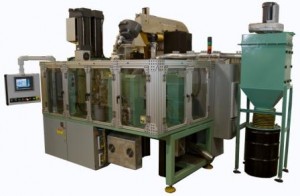
Ammunition Back End Case Line Machine
Completely changing the way cases are produced, our 30’ x 30’ design includes two forming stations, a wash system, and annealing tower to provide cases ready to load.
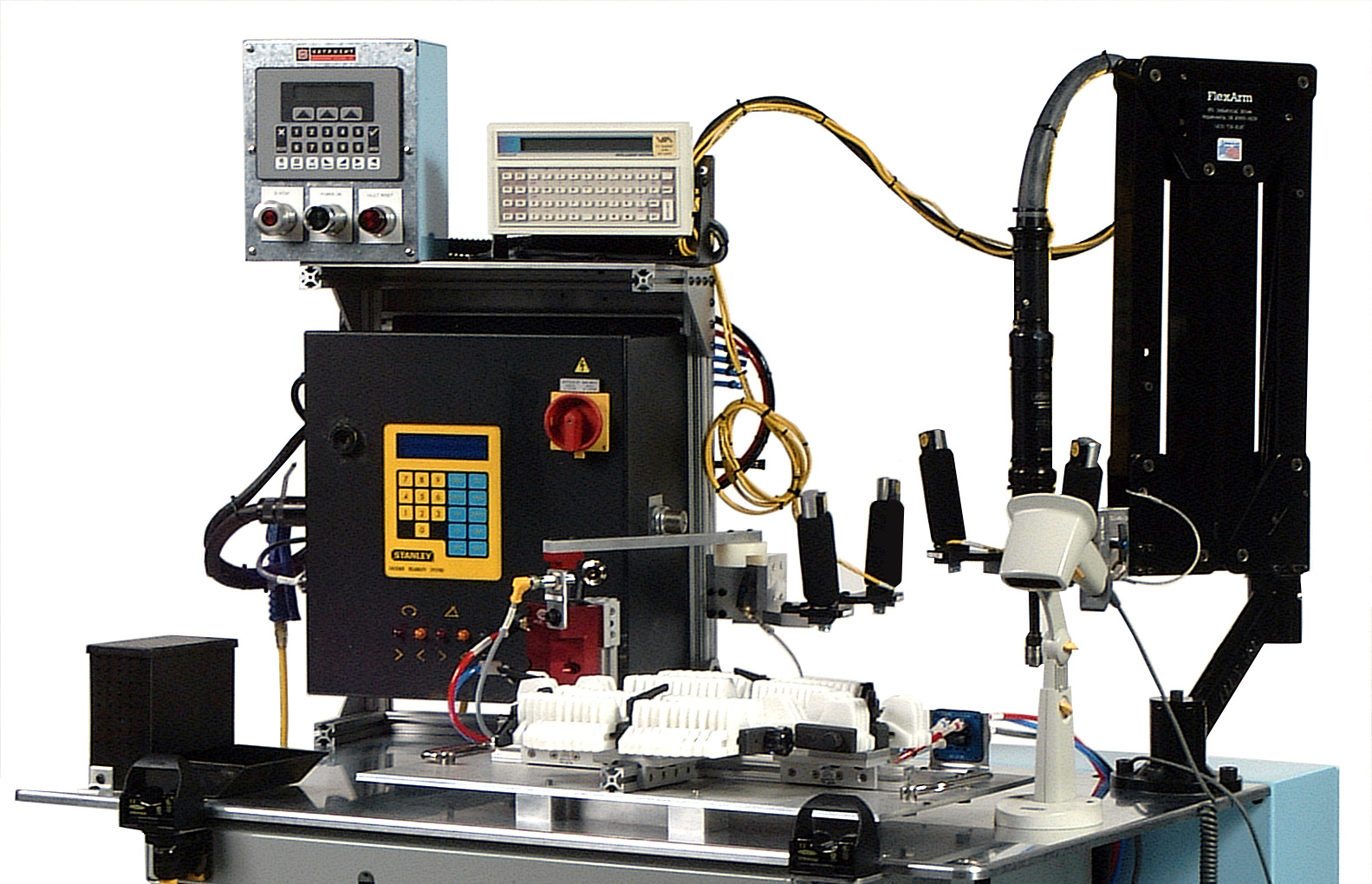
Torque Assembly
We helped significantly reduce overall labor costs and repetitive motion injuries associated with manual assembly sequences with this machine. Each station includes an articulating arm that holds the torque tooling and allows the operator to easily manipulate it into place to install each fastener.